2.74.5.1 Tutorial for Control ChartsTutorial-Control-Charts
Notes for Starting
- Download the sample project file from here and open it in Origin.
 | Topics for Further Reading:
|
Variables Charts for Subgroups: Xbar-R
Background
A manufacturer produces high-quality screw nuts that must equal 21 millimeters in diameter.
The quality control department drew 4 nuts from the finished products of two machines per day for 20 days, measured the diameters for each.
They want check whether the mean diameter to the nuts is equal to 21 and the different of their diameter can not vary more than 0.05 (20.95, 21.05), and monitor the operation of the two machines.
Steps in Origin
- Open folder 1. Normal, activate the workbook Diameter
- Click the Statistical Process Control icon
in the Apps Gallery window.
- Select the Control Charts tab, select Variables Charts for Subgroups from the dropdown list, select Xbar-R

- In the Input tab of the opened dialog, select column B and C to be Measurement Data. Choose Subgroup Size By to be Column and set the Subgroup Size Column to be Column A
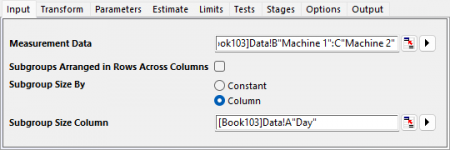
- In the Parameters tab, set Historical Mean to be 21
-
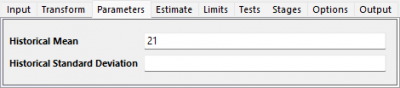
- In the Limits tab, expand the Bounds on Control Limits for Xbar Chart branch. Set Lower Spec to be 20.95, Upper Spec to be 21.05
-
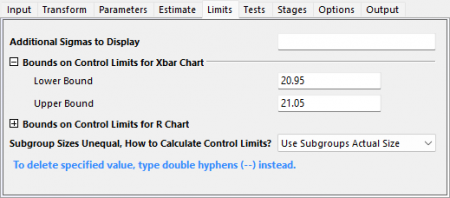
- In the Tests tab, select following Tests
- 1 Point More Than K Standard Deviation From Center Line
- K Points in a Row on Same Side of Center Line
- K points in a Row within 1 Standard Deviation of Center Line (Either Side)
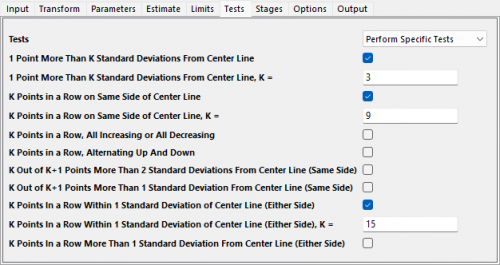
- Click OK button. A graph with report tables will be created
Interpreting the Results
Examine the R chart first, if the process variations are not in control, the Xbar Chart may be inaccurate. All the points are within the control limits in the R chart of the two machines, the process variation of the two machines are in control.
Machine has 1 out-of-control points. The Xbar chart of machine 1 indicate that there is a point is beyond the control limits for Machine 1. The test result of TEST 1 also reported that Test 1 is fail at point 18
Machine 2 is still in control. All the points are within the control limit of Xbar chart of machine 2.
Variables Chart for Individuals: I-MR
Background
A quality engineer wants to evaluate the pipe production process. He collected data for height (feet) of pipe at 150 samples. He wants to know whether the height of pipe is still in control.
Steps in Origin
- Open folder 1. Normal. Activate the workbook Height of Pipe.
- Highlight column A in worksheet. Click the Statistical Process Control icon
in the Apps Gallery window.
- Select the Control Charts tab, select Variables Charts for Individuals from the dropdown list, select I-MR
- # In the Input tab of the opened dialog, column A is selected automatically as Measurement Data.
- In the Tests tab, select following Tests
- 1 Point More Than K Standard Deviation From Center Line
- K Points in a Row on Same Side of Center Line
-
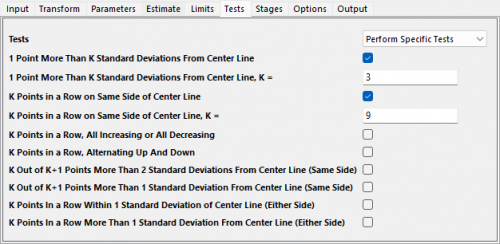
Interpreting the Results
Check the MR chart first. In addition the notes says point 82 and 133 failed Test 1, and point 105 failed Test 2. The process variation may be not so stable.
Attributes Charts: P Chart Diagnostic and P
Background
The manager of a shop performs service satisfaction survey every day for 25 days and mark down the number of unsatisfied users.
He wants to know how well the service meets specifications.
Steps in Origin
- Open folder 4. Binomial, activate the workbook Survey
- Click the Statistical Process Control icon
in the Apps Gallery window.
- Keep in the Control Charts tab, select Attribute Charts from the dropdown list, select P-Chart Diagnostic
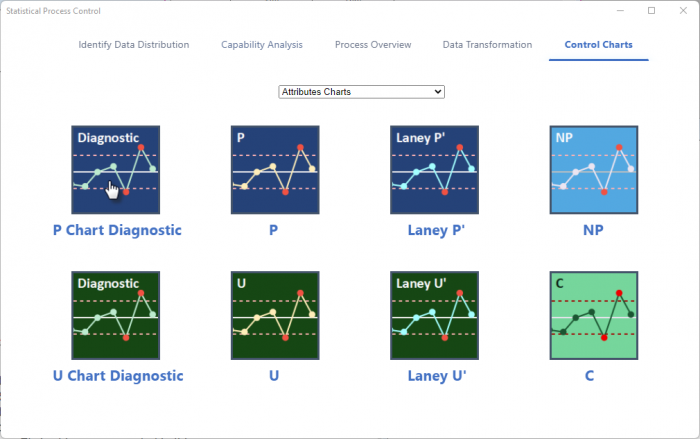
- In the Input tab of the opened dialog, set Defectives to be column B. Choose Sample Size By to be Column and set the Sample Size Column to be Column A
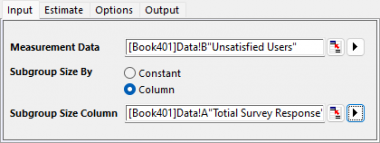
- Click OK button. A graph is created
-
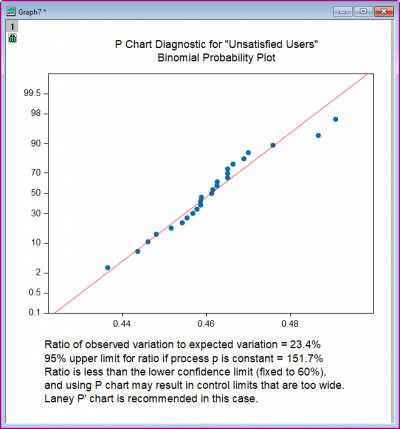
- As mentioned in the notes of the P Diagnostic chart. Laney P' chart should be used. Click the Statistical Process Control icon
in the Apps Gallery window.
- Keep in the Control Charts tab, select Laney P'
- In the Input tab of the opened dialog, set Defectives to be column B. Choose Sample Size By to be Column and set the Sample Size Column to be Column A

- In the Input tab, seelct Perform All Tests from the Tests drop-down list
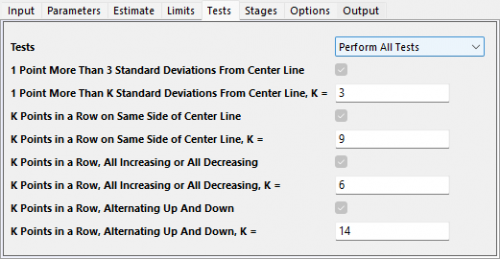
Interpreting the Results
All data points fall within the control limits. while the note has no content for points failed, which means all tests are passed. The process are in control
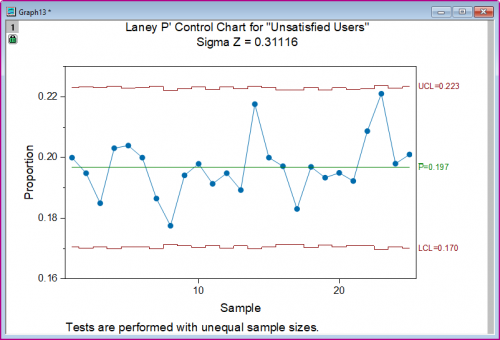
Time-Weighted Charts: CUSUM
Background
A manufacturer produces high-quality screw nuts that must equal 21 millimeters in diameter.
The quality control department drew 4 nuts from the finished products of two machines per day for 20 days, measured the diameters for each.
They want check whether the mean diameter to the nuts is equal to 21 and the different of their diameter can not vary more than 0.05 (20.95, 21.05), and monitor the operation of the two machines.
The quality control department has already created X-Bar chart in X-Bar chart part. However, they also want to monitor the machine wear of these machines
Steps in Origin
- Open folder 1. Normal, activate the workbook Diameter
- Click the Statistical Process Control icon
in the Apps Gallery window.
- Select the Control Charts tab, select Time-Weighted Charts from the dropdown list, select CUSUM
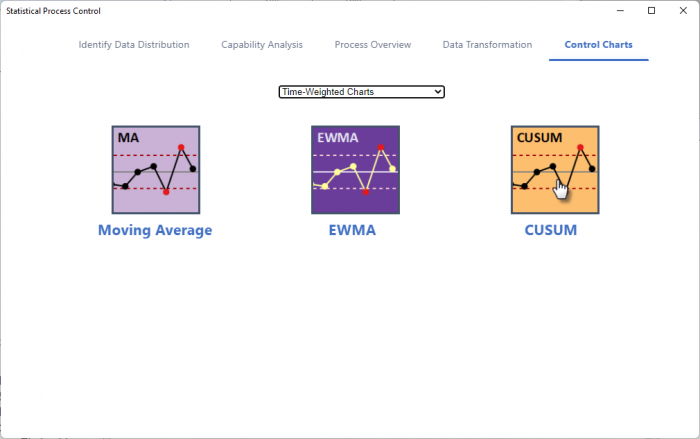
- In the Input tab of the opened dialog, select column B and C to be Measurement Data. Choose Subgroup Size By to be Column and set the Subgroup Size Column to be Column A. Set Target to be 21
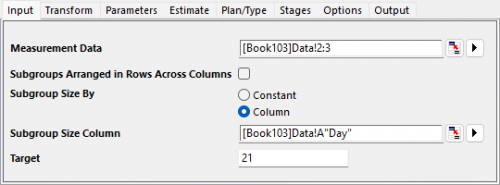
- Click OK button. A graph is created
Interpreting the Results
For machine 2, all points are in control in the CUSUM chart.
For machine 1, the process starts to have small shift from points 17. The manufacturer should check whether machine 2 is worn out during time.
|